PCD saw blade is a high-efficiency cutting tool. It has been widely used in various industries such as furniture, lumber, construction, decoration, renovation, non-ferrous metallurgy, etc. It can be used to process various soft and hard natural woods and artificial boards such as particleboard, plywood, fiberboard, laminated board, as well as various non-metallic materials such as aluminum alloy profiles, plastics, plastic-steel doors and windows, plexiglass, fiberglass, etc.
.jpg)
PCD saw blades are particularly suitable for cutting laminate flooring. In recent years, in China the laminate flooring processing industry has developed rapidly, with an annual output of over 100 million cubic meters, ranking first in the world. Since all the cutting processes of laminate flooring processing use circular saw blades, the market demand for PCD circular saw blades is quite large. In the past, most of the cutting processes of laminate flooring used carbide circular saw blades. Since there is an A0 wear-resistant layer on the surface of laminate flooring, its hardness is extremely high, and the wear of carbide circular saw blades during processing is quite large. A carbide saw blade can usually only process dozens of large boards before the cutting edge becomes blunt and must be sharpened. The PCD circular saw blades developed in recent years have the advantages of high cutting speed, good wear resistance, low noise, high efficiency, good processing quality, high smoothness of the processed surface, and no edge collapse of the board. An ultra-thin PCD saw blade can process 8,000 to 10,000 large boards, and its durability is hundreds of times that of carbide saw blades. Therefore, it is gradually replacing traditional carbide saw blades, and its market prospects are very broad.
Since the ultra-thin PCD circular saw blade is a new type of cutting tool with high efficiency, it has the characteristics of ultra-thin, large diameter, complex tooth shape and high precision, and it is more difficult to process and make, in the past, only a few foreign tool companies can produce. After scientific and technological research and experimental development, 3Better ultra-hard materials Co., Ltd has mastered the processing and production technology of ultra-thin PCD circular saw blade, and has achieved mass production.
1.Main technical parameters of ultra-thin PCD circular saw blades:
Diameter: 150~350mm; number of teeth: 40~80Z (PCD); tooth width: 1.8~2.5mm; base thickness: 1.4~2mm; rotation speed: 3800~5000r/min; cutting thickness: 20~60mm.
.jpg)
2 Selection of saw blade substrate material
The substrate is the carrier of the PCD blade. Since the PCD circular saw blade substrate is very thin (1.5~1.8mm) but has a large diameter (150~350mm), the linear speed during cutting can reach 50~100m/s, and the cutting thickness can reach more than 60mm. Therefore, the saw blade must withstand high temperature, strong impact, extrusion, distortion, friction, etc. during use, and the use environment is very harsh. A large amount of industrial adhesive in the saw blade substrate is easily melted by heat and adheres to the PCD blade, increasing resistance and affecting processing. In severe cases, it causes deformation of the substrate and even fracture of the tooth back. Therefore, the mechanical properties of the saw blade substrate are very high. It is necessary to comprehensively consider the flatness, rigidity, toughness and other aspects to correctly select the substrate material. In addition, the deformation of the substrate after welding is required to be as small as possible. Generally speaking, the hardness of the saw blade substrate is preferably 42~48HRC. It is not acceptable to be too high or too low. Materials such as 75Cr1.65Mn are more suitable as saw blade substrates. At present, due to problems with the heat treatment process, saw blades made with domestic base materials often experience tooth back breakage after a period of use. Further research and improvement of the heat treatment process of the base material is needed. However, similar problems rarely occur with imported base materials.
3. Selection of PCD blade models
The selection of PCD blades for saw blades should match the material of the work piece being processed. Because the wear resistance and strength of different types of PCD blades will be quite different, only by correctly selecting the appropriate PCD blade according to the material of the work piece can a relatively ideal processing effect be achieved.
4. PCD saw blade welding
Low-temperature welding technology should be used and the welding temperature should be strictly controlled. Ultra-thin PCD circular saw blades have narrow teeth and small welding surfaces, which are not easy to weld firmly. They have high requirements for silver solder and flux. In order to meet the left-right symmetry of the blade and the substrate, it is best to use an automatic laser welder for welding. Stress relief should also be performed after welding to reduce deformation.
5. Cutting Angle and Tooth Profile
The cutting angle and tooth profile of PCD saw blades directly affect the processing quality and life of the saw blades. The commonly used cutting angles of PCD saw blades are: front angle y: 5~15°; back angle a: 10~18°; side back angle 3~5°. The tooth profiles of PCD saw blades include flat teeth, left helical teeth, right helical teeth, trapezoidal teeth, arc teeth, triangular teeth, conical teeth, etc. (see Figure 1), and these tooth profiles usually need to be used in combination. In general, the tooth profiles of two adjacent teeth of PCD saw blades are different, and the tooth heights are also different. For example, in the combination of flat teeth and trapezoidal teeth, the trapezoidal teeth are 0.2~0.3mm higher than the flat teeth. Therefore, it is necessary to select the optimal cutting angle and tooth profile combination according to different machine tools, different processed materials, and different requirements of different customers.
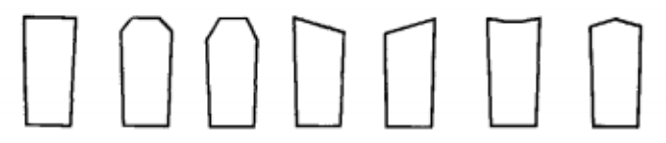
6. Sharpening of PCD saw blades
Sharpening of PCD saw blades is a very critical process. The accuracy and dimensional tolerance of the saw blade tooth profile are strictly required: the outer circle tooth top runout is ±0.015mm; the side runout is +0.025mm; the adjacent teeth runout is ±0.01mm, and the roughness R<0.3um. Mechanical sharpening cannot meet the above requirements at all, and special PCD CNC EDM equipment must be used for processing. Generally, the two sides are processed first, and then the back angle is processed. Two methods can be used: external circular discharge and end face discharge. Because the saw blade has many and dense teeth (40~80Z), interference must be prevented during processing, and the tooth profile must be sharpened symmetrically relative to the base, otherwise the uneven force on both sides will easily cause the PCD circular saw blade to wear too quickly and reduce its life.
This is our latest product launch. The price/performance ratio is very high. If you want to know more detailed product parameters and price. You can send email to contact us. sales@3betterdiamond.com