There are various styles and specifications of diamond grinding wheels to fit various application requirements. The ones with many big diamond segments can undertake heavy workloads, for example, grinding concrete and stone, while those with small or sparse diamond segments are normally used for fast removal of paints, wallpapers, glues, epoxy and other surface coatings.
Just like other metal-bonded diamond tools, the diamond segments on diamond grinding wheels can have different bonds, different diamond grits, different diamond quality and different diamond concentrations to fit different uses. For example, if the material to be ground is hard, the bond should be softer, and if the material is relatively soft, the bond should be harder.
Diamond grinding wheels are used in different-roughness grindings. For coarse grinding, the bond should be softer and the diamonds' quality should be higher, because in this case the diamonds become blunt more easily. The diamond grit should be bigger, normally from 35 grit to 50 grit. For this is coarse grinding and big grit can improve working efficiency. The diamond concentration can be lower.
For fine grinding (sometimes called "polishing"), the bond should be harder and the diamonds' quality can be lower, as in this case the diamonds can last longer and a hard bond can also help the precision of the process. The diamond grit is normally between 80 grit and 120 grit, depending on the grinding requirements. The diamond concentration should be higher.
After being ground, the material can be further polished with resin-bonded diamond polishing pads of different diamond grits.
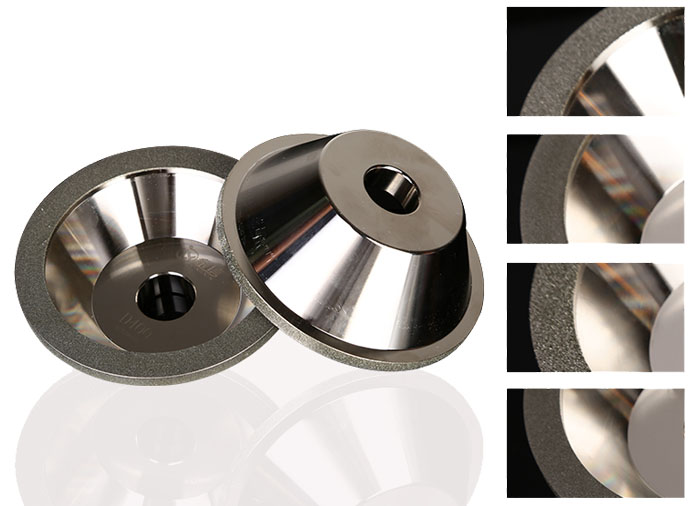